Silk is widely recognized at the premium fabric through history. The inception of this fabric originated in ancient China. Initially, the Chinese were highly secretive about the process of making silk. Indeed, the reigning powers decreed death by torture to anyone who divulged the secret of the silk-worm. However, the process was later uncovered by neighboring nations like japan and later India
Currently India is the second largest producer of silk behind China. India has a rich history of silk as well. It’s colloquially known as Resham in eastern and northern. India and pattu in the southern areas of the nation. Raw mulberry silk is found in six Indian states and contribute to 97% of total production.
Since silk is a natural fiber, it is inherently sustainable and non-damaging to the environment. The harvesting and production of wild silk does not have any negative environmental impact.
Further, it is highly valued because it possesses many excellent properties. Not only does it look lustrous and feel luxurious, but it is also lightweight, resilient, and extremely strong—one filament of silk is stronger then a comparable filament of steel
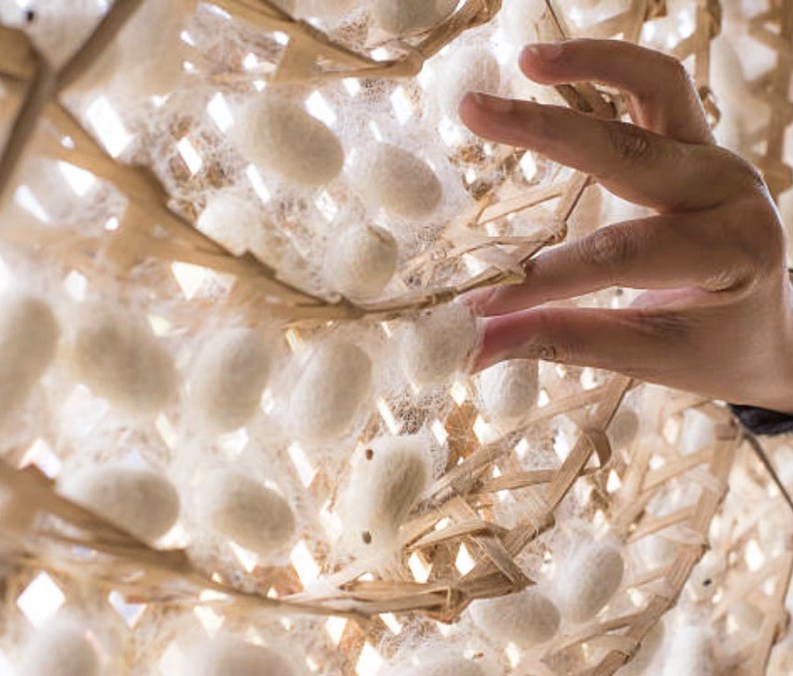
Harvesting
Extracting raw silk starts by cultivating the silkworms on mulberry leaves. Once the caterpillars are 10,000 times heavier than when hatched, they are ready to begin spinning a cocoon. The cocoons are carefully picked by hand to ensure that no damage is done to the delicate silk fibers.
Stifling & Sorting
A fully formed pupa is hard and brown in color. To stop the pupa inside the cocoons from hatching and breaking the silk cocoon, it needs to be heated with hot air or steam(stifling). Some pupa are left alive to metamorphose into moths to breed the next generation of caterpillars
Stifling also dries out the cocoon so that it can be preserved longer. The cocoons can then be sorted based on quality and characteristics such as the length, shape, color, and luster of the silk fiber.
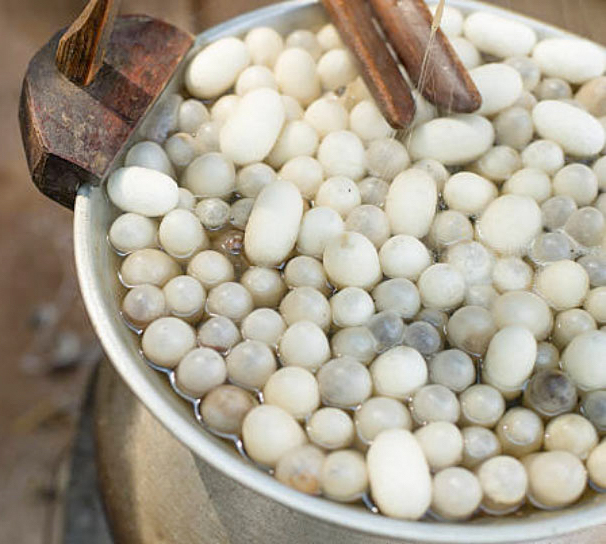
Boiling
Then the cocoons are dissolved in boiling water to extract individual long fibres. This process also degums the silk by removing sericin. Boiling softens the hard sericin protein and makes the cocoons smoother in texture and feel, therefore softening the silk.
Deflossing
After boiling, the surface of the cocoons may still be covered in some loose fiber, making the cocoons look fuzzy. This fuzzy layer consists of broken and uneven silk filaments. The loose fiber is removed from the cocoons in a process called deflossing. The fibers are then unwound to produce a continuous thread. Deflossing gives the cocoons a clean look, makes it easier to process the cocoons further, and increases its market value.
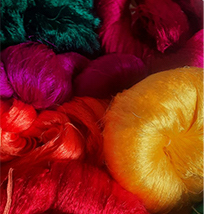
Reeling
Reeling is the unrolling of the cocoon and the combining of multiple silk filaments into one single strand of silk. A single strand of silk is too thin to use on its own, therefore filaments of multiple cocoons are reeled together to create one strand of silk yarn. The number of cocoons reeled together can be anywhere from 2 to 20, depending on the desired thickness of the silk yarn.
As silk fibers are so fine and light, you need about 2500 cocoons to produce 1 pound of silk!
Twisting & Dying
The silk is twisted into spiral circles to form bundles ( also known as skeins.)
After twisting, the silk yarn is ready to be dyed. Silk is easy to dye due to the structure of the fibroin proteins that make up most of the silk. Silk easily absorbs dye making the colors look vibrant.
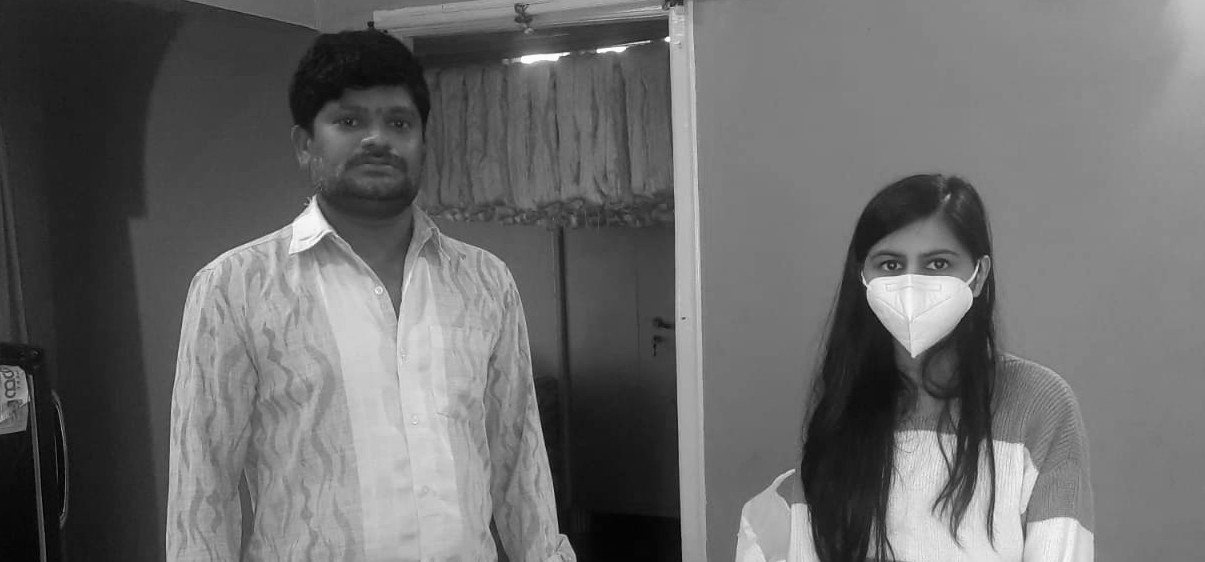
Lokesh's family has been making pure silk for generations. His grandfather used to make silk on handlooms at the time when every 1 family in 5 used to produce silk in the Domlur region. Today, that number has reduced drastically and Lokesh is among the few remaining artisans who still produce pure silk.